Mastercam 2025 Public Beta
Mastercam 2025 version Beta has been released and is available for download for all Mastercam maintenance customers from my.mastercam.com at https://downloads.mastercam.com
Mastercam 2025 introduces many new features that make programming easier and faster than ever before. With the new Mastercam 2025 version, you can create the same program with fewer toolpaths than with the software's previous versions. Taking fixtures into account in operations ensures even more reliable toolpaths, and new operations increase opportunities to gain a competitive advantage by using the latest methods and tool innovations.
The new features in Mastercam 2025 include:
2D Dynamic Milling and Area Milling Finish Passes
A much-awaited feature for the popular 2D Dynamic Milling and Area Milling are their finish passes. Thanks to the finish passes, finishing the shapes is easy with the same operation when finishing the shape with the same tool. Finish passes also allow for pre-finishing of shapes with CNC control compensation, leaving the same material allowance for the final finish with resharpened tools.
Fixture Geometry in 3D Operations
Considering workpiece fixtures during programming helps to achieve more ready-to-use machining programs and prevents costly collisions on CNC machines. In the new Mastercam 2025 version, taking fixtures into account for all 3D operations is now even easier. Fixtures specified once in a job setup are directly visible on the 'Model Geometry' tab of operations.
Plane Display Settings
The new transition parameters introduced in Mastercam 2024 for drilling operations are now available in all modern 2D machining operations. The new advanced transition parameters can be controlled not only from menus but also from the Mastercam screen area, making it easy to move the height of different machining planes visually. Graphical plane displays always provide a preview of selected transition parameters. The new transition parameters also include the previously separate 'piercing' option, which means the piercing selection does not need to be defined separately on another tab.
3-Axis Deburring Operation
The deburring operation known from multi-axis toolpaths is now part of the Mill3D license as a 3-axis version. The deburring function automatically removes burrs with radius and ball nose mills from all edges of a Solid model. The deburring function can also avoid specified geometries to avoid, such as workpiece fixtures.
Y-Axis Turning and A-Axis Turning
Mastercam 2025 Mill-Turn now also supports Y-axis turning in all traditional turning operations as well as advanced operations such as dynamic turning and PrimeTurning™. Y-axis turning is an extremely stable method because the cutting forces are primarily directed toward the machine spindle during the process. In grooving and parting operations, using the Y-axis reduces the load on the parting blade, making it possible to use higher feeds and longer free lengths on the parting blades.
A-axis turning refers to Y-axis turning where the tool rotates around the tool axis (A-axis) during the turning path. Compared to B-axis turning, A-axis control during the toolpath requires much smaller movements from the machine, resulting in a stable and accurate machining process. A-axis control during the turning path allows the tool's set angle to be maintained constant relative to the shape being turned, achieving a stable machining process and optimal control of the cutting chips. A-axis turning enables the turning of complex parts with a single tool and a single chip without the junctions of different tools and operations.
Mastercam 2025 will be released later this year. You can also explore the current and upcoming version of Mastercam at the Machine Shop 2024 event at Camcut Oy's booth A722.
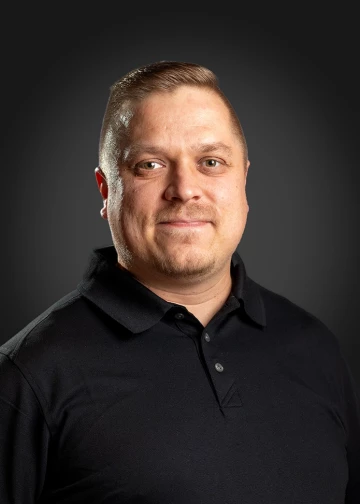